Greatest possible flexibility for your requirements
Do you want to pack your cement, building material or chemical products in valve bags or FFS (Form, Fill, Seal) open-mouth bags? Do you want to pack your products at a rate of between 300 and 1,200 bags/hour (5-40 bags/min)? Then you’ve come to the right place. The INTEGRA® is our packaging machine that integrates all components in an enclosure and can be used Plug & Play.
Five good reasons why you should choose an INTEGRA®:
- Plug & Play - the housed and complete packaging system for every product and every container
- High-quality standard equipment configurable for every requirement
- Versions for valve or tubular film bags
- Worldwide OEM-own full service and supply with original spare parts and conversion kits
- Optionally expandable with full digital equipment for monitoring, remote and diagnostics
The INTEGRA® IV series for valve bags
Pack your powder, flour-type or granular products into valve bags with the INTEGRA® IV series, with 1 to 4 filling spouts. These can be made of paper, woven PP or PE. The filling system , completely assembled in a dust-enclosed housing and consists of:
- packing machine
- bag applicator
- control technology
- control panel
- bag discharge belt
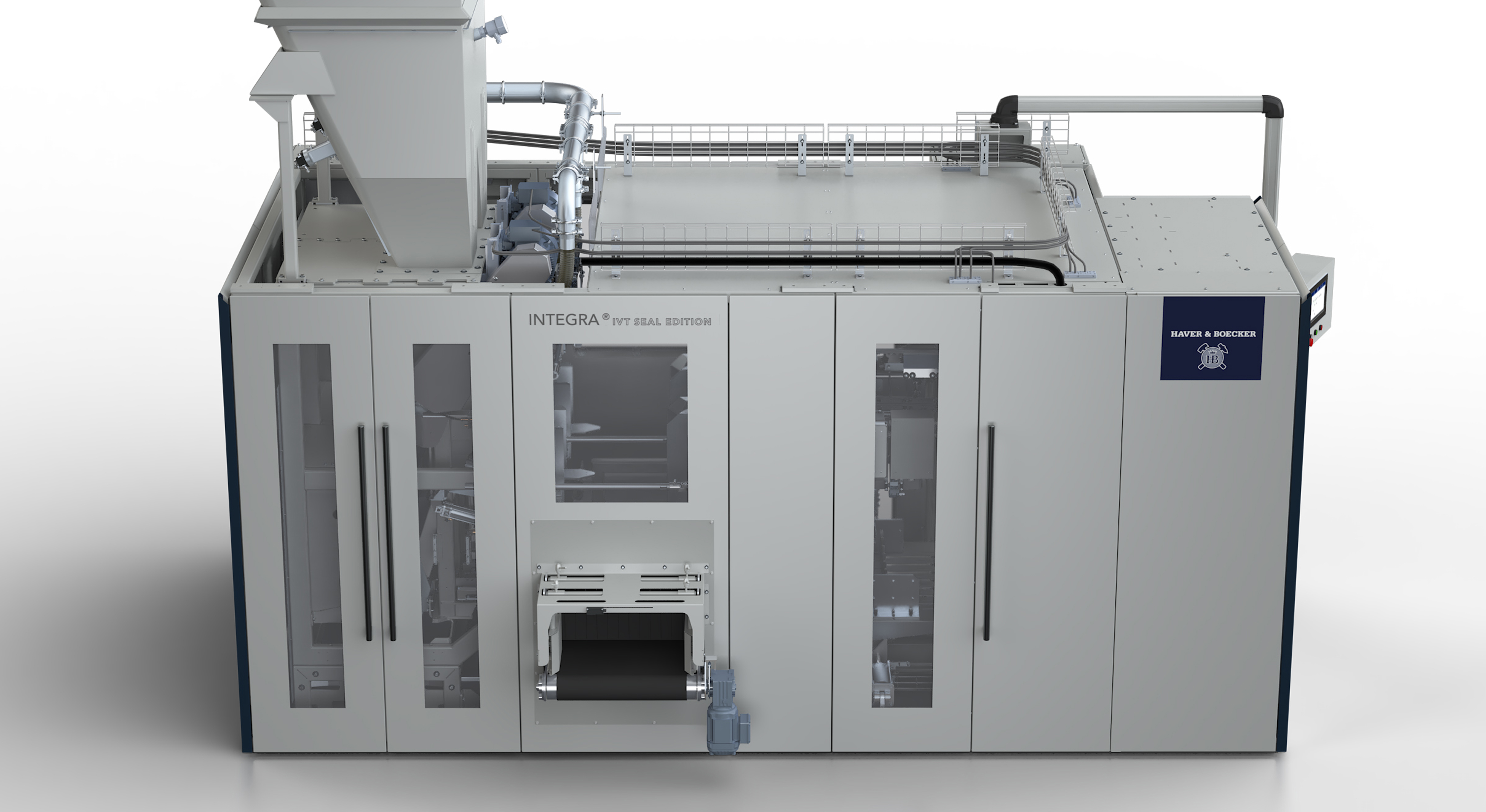
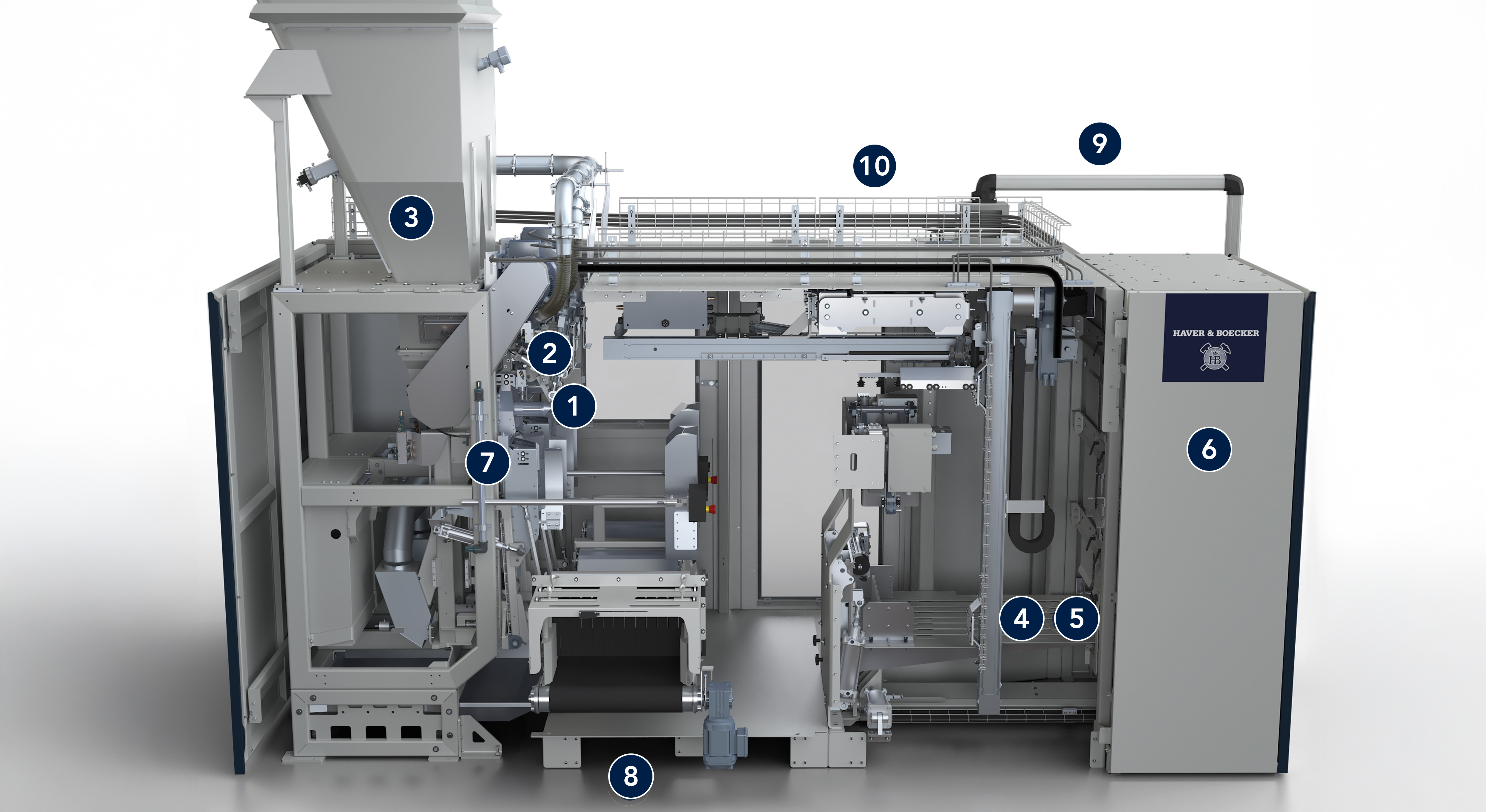
HAVER & BOECKER INTEGRA® - Plug 'n Pack
Steamed machine noise, clean working environment: thanks to our Plug 'n Pack concept, the entire plugging, filling and closing process of the valve bags takes place in a dustproof encapsulated cabin.
New standards
1. reduced overall energy consumption
2. higher performance
3. cleaning-optimized design
4. improved accessibility
5. flexibility in use
- 6 Smart and digital solutions
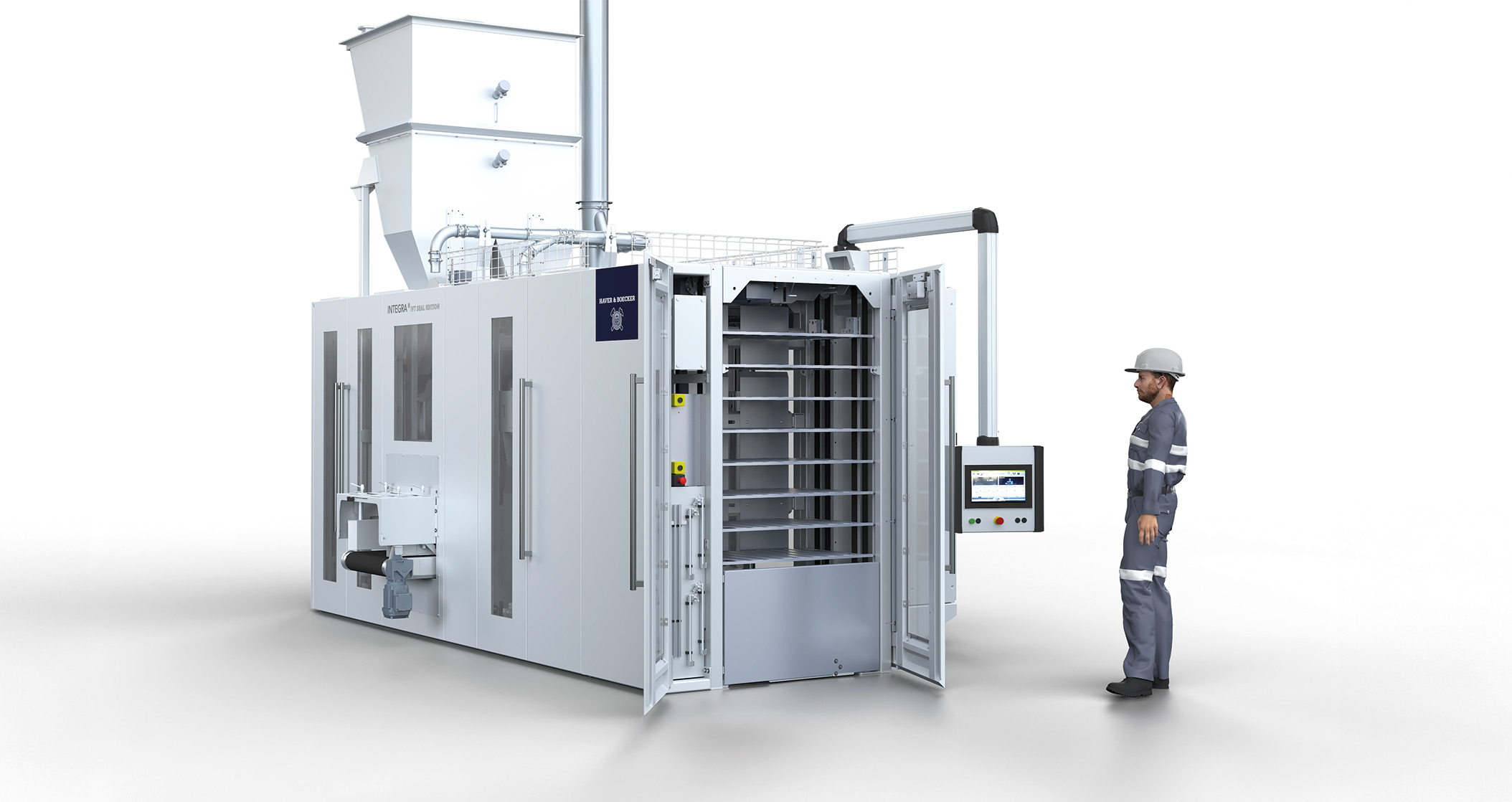
New modern HMI
-
15,6‘‘ Full HD
-
Remote access via PC, smartphone, tablet and browser
-
ATEX certificated (optional)
-
PDF and website display possible
-
Customizable login
-
System messages with comment function
-
New recipe management
-
Logbook function
-
Switch of HMIs within a line
-
Multi-touch - swipe and zoom function
Energy efficiency
-
Reduced total energy consumption by up to 2.5%
-
Energy-saving and switch-off mode for process units
-
Utilization of braking energy
-
Optimized dust extraction volume
Maximum availability
-
Wear-free servo drives
-
Use of OEM identical parts and systems
-
Assured spare parts supply
Increased performance
-
Up to 10% higher performance
-
Faster cycle due to diagonal movement of the attachment arm
-
AI-supported camera technology for optimized attachment rate (optional)
User-friendliness
-
15.6-inch touch control panel
-
Modern, web-based HMI
-
Standardized operating concept
-
Tidy interior design and large window
-
Diagnostic lighting (optional)
-
RFID sticks
-
MEC IV weighing control device
Improved accessibility
-
Swivel-mounted control cabinets (optional)
-
Protected cable routes on the roof
-
Simple settings thanks to pneumatic shaft
-
Transformer function (optional)
-
Large openings and doors
Easy maintenance
-
Centrally arranged pneumatics, also accessible during operation
-
Easy-to-open, accessible cladding elements
-
Cleaning-optimized positions in maintenance mode
Flexibility in use
-
For every HAVER & BOECKER filling system with 1-4 filling spouts
-
Larger range of bag lengths and widths
-
New clip-on claw for different valve sizes
-
Three magazine variants for empty bags
-
Standardized motor system
-
Suitable for hygiene and pharmaceutical applications
-
Variable arrangement of the spouts
-
Separate installation of control panel (optional)
Hygiene and cleaning
-
Up to 50% time saving during cleaning
-
Cleaning-optimized design of the bundle magazine (optional)
-
AI-supported camera technology for fewer bag bursts (optional)
-
Systems for various hygiene applications
-
Hygienic design and installation
Smart and digital solutions
-
digital QUAT'RO® solutions (optional)
-
AI-supported process performance
-
modern, web-based HMI
The INTEGRA® IS series for tubular film
Pack your powder, flour-type or granular products into open-mouth FFS (form, fill, seal) bags with the INTEGRA® IS series, with 1 to 4 filling spouts. The filling plant for building material, minerals or chemical products, completely assembled in a dust-enclosed housing, consists of these components:
- packing machine
- Bag production and handling
- control technology
- control panel
- bag closure and discharge belt
Step 1 - Choose your filling module
The properties of your product determine the filling module. If you’re packing fine powder, you’ll choose the T-module. The "T" stands for "turbine", which means impeller. The product is transported into the bag by means of an impeller. The T-module is available in vertical and horizontal versions. If you’re packing mixed products that differ in grain size, select the L module. "L" stands for "air". In this process, the product is conveyed from the pressure chamber into the bag by means of air pressure. The L-module is available in two versions, either with an angled or a fully ventilated base plate in the pressure chamber.
We offer the turbine filling technology and the air filling technology as a VT module and a VL module for the use of valve bags and as a ST module and a SL module for the use of tubular film.
The two IV modules are available in a standard version or as a SEAL upgrade to weld the valve shut after the filling process. The T-module can be equipped with standard sliding plates or the patented ROTO-LOCK® dosing system. The two IS modules are equipped with either a vibrating rod or a vacuum rod to optimize de-aeration during the filling process.
Step 2 - further options
- Automatic saddle height adjustment: for different bag lengths and frequent changes
- QUAT²RO® monitoring: Track the current status of your machine and create reports from your smartphone or any internet-enabled computer.
- QUAT²RO® remote service: Let us support your team in servicing the machine.
- QUAT²RO® analytics: Analyse your production process to optimize performance.
Did you know...?
If you take the word "racing" in Ayrton Senna's famous words "Racing, competition, is in my blood. It's a part of me, it is a part of my life ..." and replaced by the word "packing", you have essentially captured the spirit of HAVER & BOECKER. The day we decided to create a concept that housed all packaging functions in just one machine housing, we knew that speed was essential. Coordinating all the movements so that they run in sync, at the limit of what is technically possible, reminded us of the challenges of motorsports. That is why the racetrack has come to symbolize the INTEGRA®.
Henrik Knoche
![[Translate to English:]](/fileadmin/HaverBoecker/DieMaschinenfabrik/01_graphic/Neue_Profilbilder/henrik-knoche.png)
Henrik Knoche
Business Unit Building Products and Minerals
Alexander Hering
![[Translate to English:] Alexander Hering](/fileadmin/PortlandCompany/user_upload/Alexander_Hering.png)
Alexander Hering
Business Unit Cement
Daniel Denisow
![[Translate to English:] Daniel Denisow](/fileadmin/HaverBoecker/DieMaschinenfabrik/01_graphic/Neue_Profilbilder/Daniel_Denisow.png)
Daniel Denisow
Business Unit Chemicals