Your challenges determine our technology
Do you want to pack your cement, building materials or chemical products in valve, open-mouth or FFS (Form, Fill, Seal) bags? Do you want to pack your powder with a capacity between 400 and 6,000 bags/hour (7-100 bags/min.)? Then you’ve come to the right place. The original ROTO-PACKER® is the most advanced packaging machine for industrial goods of our time.
Five good reasons why you should choose the original:
- The rotating high-performance packaging system for industrial bulk materials - successfully established on the market
- High-quality standard equipment configurable for every requirement
- Versions for valve or tubular film bags
- Worldwide OEM-own full service and supply with original spare parts and conversion kits
- Optionally expandable using full digital equipment for monitoring, remote and diagnostics
The ROTO-PACKER® RV series for valve bags
The ROTO-PACKER® RV series with up to 16 filling spouts packs your cement, building material or chemical products into valve bags with a capacity between 1,000 and 6,000 bags/hour. (17-100 bags/min.). The valve bags can be made of paper, woven PP or even film. The automatic packaging machine can be upgraded with an ultrasonic sealing device. The packaging is safe, clean and profitable.
The ROTO-PACKER® RS series for tubular film
The ROTO-PACKER® RS series, with up to 10 filling spouts, packs your cement, building material or chemical products into open, formed, filled and closed (FFS) bags at a rate of between 400 and 1,200 bags/hour (7-20 bags/min.), using ADAMS® technology. The result is fully recyclable packaging with excellent protection for your product from the elements. In other words: The ADAMS® film bag is weatherproof, safe and profitable.
Step 1 - Choose your filling module
The properties of your product determine the filling module. If you are packing fine powders, you’ll choose the T-module. The "T" stands for "turbine", which means impeller. The product is transported into the bag by means of a turbine. The T-module is available in vertical and horizontal versions. If you are packing mixed products that differ in grain size, select the L module. "L" stands for "air". In this process, the product is conveyed from the pressure chamber into the bag by means of air pressure. The L-module is available in two versions, either with an angled or a fully ventilated base plate in the pressure chamber.
We offer the turbine filling technology and the air filling technology as a VT module and a VL module for the use of valve bags and as a ST module and a SL module for the use of tubular film.
The two RV modules are available in a standard version or as a SEAL upgrade to weld the valve shut after the filling process. The T-module can be equipped with standard sliding plates or the patented ROTO-LOCK® dosing system. The two RS modules are equipped with either a vibrating rod or a vacuum rod to optimise deaeration during the filling process.
Step 2 - Choose your options
- ROTO Adjust: Adjust the bag saddle heights to different bag sizes automatically
- ROTO-LOCK®: The ROTO-LOCK® completely eliminates spillage during the dispensing process and requires almost no maintenance.
- RADIMAT®: place your bags automatically
- QUAT²RO® Monitoring: Communicate with your machine continuously via your smartphone or mobile device
- QUAT²RO® Scan: scan your empty bag to automatically adjust the settings in your packer to the product and packaging
- QUAT²RO® Remote: let us service your machine together with the help of a camera, smart glasses and a software connection.
- QUAT²RO® Analytics: let us permanently analyze your production process and continuously suggest performance optimizations for you
Did you know...?
The 1960s was a decade dominated by the dream of conquering space. We are proud to have contributed to this dream. Our woven wire mesh, made in our plant here in Oelde, was on board the NASA missions to the moon. Our personal interest in the success of the space voyage, as well as Neil Armstrong's words describing the lunar surface "It seems to be made of very, very fine grains as you get closer to it". Almost like a powder", are the reason why we decided that the moon is the perfect backdrop for the ROTO-PACKER®.
Michael Mestekemper
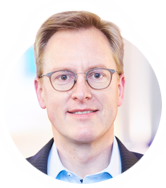
Michael Mestekemper
Business Unit Building Products and Minerals
Mirko Hoffmann
![[Translate to English:] Mirko Hoffmann](/fileadmin/HaverBoecker/DieMaschinenfabrik/01_graphic/Neue_Profilbilder/Kirko_Hoffmann.png)
Mirko Hoffmann
Business Unit Cement
Arian Shala
![[Translate to English:]](/fileadmin/HaverBoecker/DieMaschinenfabrik/01_graphic/Profilfotos/arian-shala.png)
Arian Shala
Business Unit Chemicals